Устройство подшипника изучаем конструкцию, состав и виды этого механизма
Подшипники – это основополагающие элементы многих механизмов и машин, от бытовой техники до крупномасштабного промышленного оборудования.
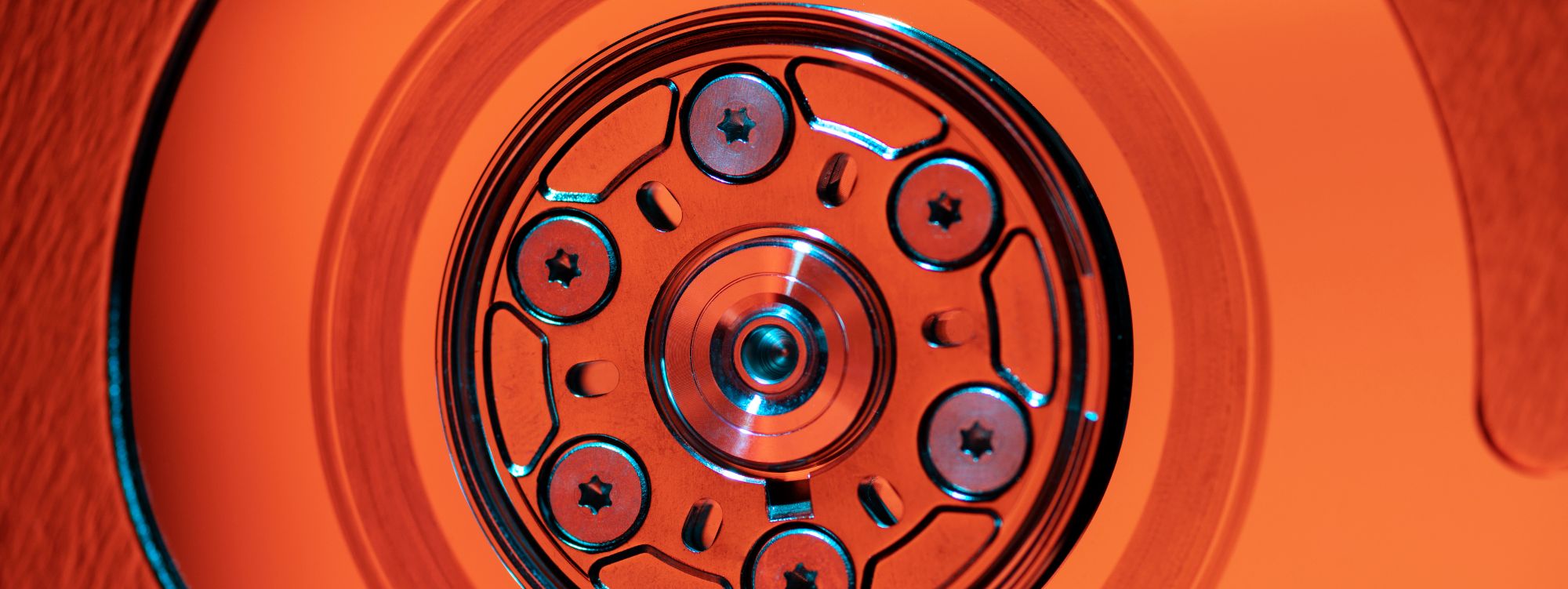
Устройство
Подшипники спроектированы таким образом, чтобы обеспечивать свободное вращение или скольжение частей машин, делая это с минимально возможным сопротивлением. Такая возможность играет критически важную роль в снижении трения между движущимися частями, что напрямую влияет на уменьшение износа и повышение общей эффективности работы оборудования.
Обзор
Шарики распределены равномерно с помощью сепаратора, который предотвращает их соприкосновение и обеспечивает стабильность их движения. В среднем, диаметр шариков может варьироваться от 1 мм до нескольких сантиметров в зависимости от размера и предназначения.
Подшипник скольжения, в отличие от шарикового, не имеет тел качения. Он состоит из гладкого внутреннего кольца (втулки), которое скользит непосредственно по валу или оси. Материалы выбираются таким образом, чтобы минимизировать трение и износ, зачастую это бронза, полимеры или композитные материалы.
Анализ состава
Изделие состоит из нескольких основных компонентов, каждый из которых выполняет свою важную функцию.
Внутреннее кольцо напрямую контактирует с валом и служит опорой для тел качения. Оно передает нагрузку от вала к телам качения, а затем — к внешнему кольцу. Материалы для изготовления внутренних колец выбираются с учетом требований к прочности, износостойкости и устойчивости к коррозии.
Внешнее кольцо фиксируется в корпусе машины или устройства и служит для передачи нагрузки. Это кольцо вместе с внутренним кольцом формирует дорожки качения для тел качения. Такая конструкция позволяет равномерно распределить нагрузку и обеспечить стабильное вращение или скольжение.
Тела качения являются основой работы изделия, обеспечивая минимальное сопротивление при вращении внутреннего кольца относительно внешнего.
Сепаратор играет критически важную роль, разделяя тела качения и обеспечивая их равномерное распределение по всему объему подшипника. Это предотвращает контакт между телами качения, снижая трение и износ. Сепараторы могут быть изготовлены из металла, полимеров или композитных материалов, каждый из которых выбирается исходя из условий эксплуатации.
Смазка выполняет несколько жизненно важных функций: снижает трение и износ, предотвращает коррозию и помогает отводить тепло от трущихся поверхностей. Выбор типа смазки определяется требованиями к температурному режиму, скорости вращения и нагрузкам.
Строение и схема устройства
Для шарикового типа типичное расположение составляет от 6 до 8 для малых подшипников и до 30 и более для больших размеров. Размер шариков и их количество зависят от номинальной нагрузки, которую подшипник должен воспринимать. Сепараторы могут быть изготовлены из металла (сталь, латунь) или полимерных материалов. Важным параметром является класс точности, который определяет допуски на размеры и форму компонентов, влияющие на шум, вибрацию и срок службы. Классы точности варьируются от общего назначения до высокоточных применений, где требуется минимальный люфт и максимальная надежность.
Для подшипников скольжения ключевыми параметрами являются материалы изготовления и тип смазки. Внутренние поверхности этого типа часто покрываются слоем материала с низким коэффициентом трения, такого как политетрафторэтилен (PTFE) или молибдендисульфид (MoS2), что позволяет добиться хороших антифрикционных свойств даже при отсутствии жидкой смазки. Подшипники скольжения могут быть как одно-, так и многослойными, где каждый слой предназначен для выполнения определенных функций, включая поддержку нагрузки, смазку и защиту от коррозии.
Современные модели разрабатываются с учетом специфики их применения, что включает в себя рабочие условия, температурные режимы, уровни нагрузок и требуемый срок службы. Например, авиационные подшипники изготавливаются из специальных сплавов, устойчивых к высоким температурам и нагрузкам, в то время как варианты для пищевой промышленности должны соответствовать строгим гигиеническим нормам и быть совместимыми с агрессивными средами.
Важной характеристикой является их нагрузочная способность, которая определяется как максимальная радиальная или осевая нагрузка, при которой подшипник может работать без преждевременного износа. Для шариковых типов радиальная нагрузочная способность обычно выше, чем осевая, из-за более высокой площади контакта между шариками и дорожками качения. В то же время, упорные подшипники оптимизированы для восприятия больших осевых нагрузок за счет увеличения площади контакта между телами качения и опорными поверхностями.
Виды и структура
Подшипники бывают разных типов, каждый из которых имеет уникальную конструкцию и предназначен для выполнения специфических функций в различных условиях эксплуатации.
Шариковые подшипники
Шариковые подходят для работы при высоких скоростях вращения и могут воспринимать как радиальные, так и осевые нагрузки. Они содержат шарики, которые катятся в специальных дорожках на внутреннем и внешнем кольцах.
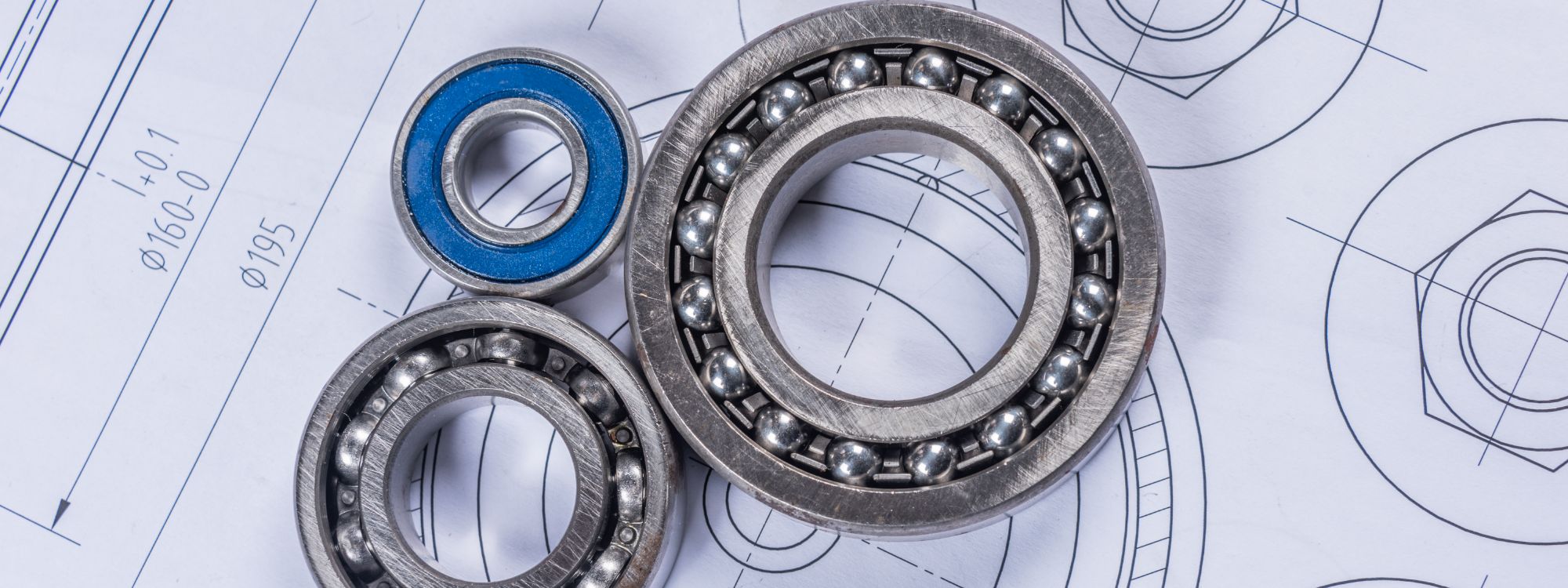
Роликовые подшипники
Роликовые при восприятии высоких радиальных нагрузок. В их конструкции используются цилиндрические ролики вместо шариков, что позволяет распределить нагрузку на большую площадь.
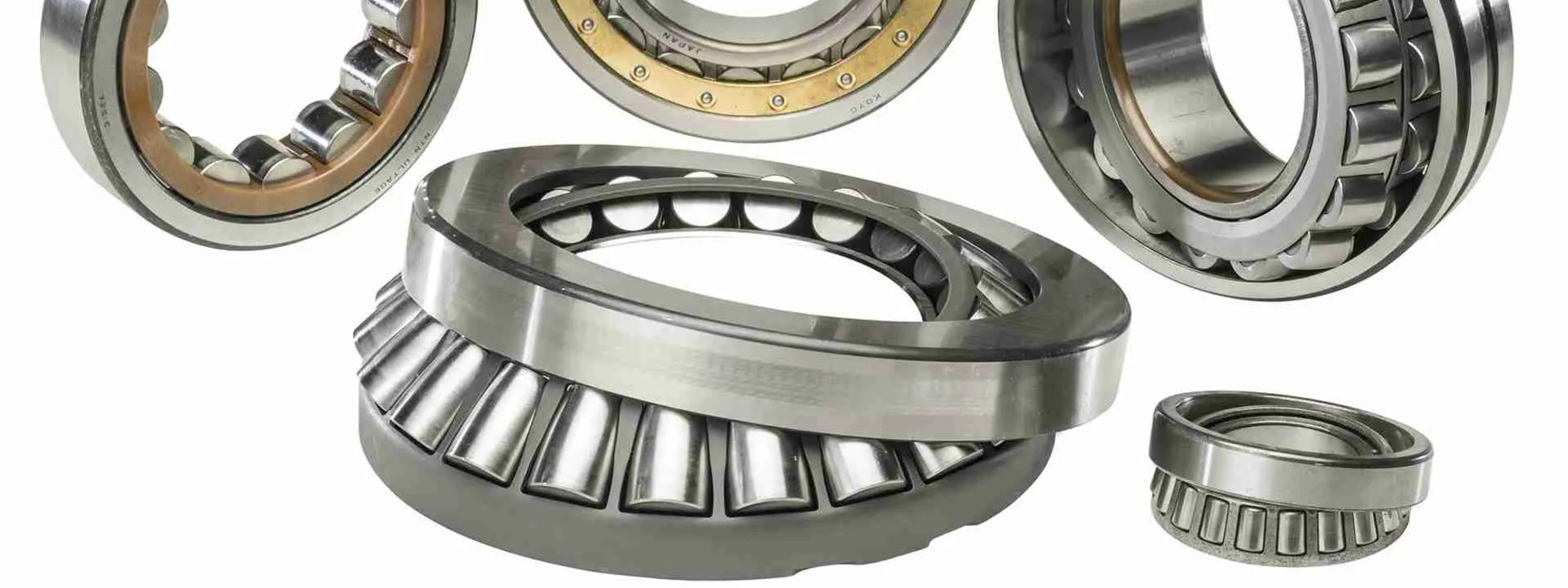
Игольчатые подшипники
Игольчатые похожи на роликовые, но имеют более тонкие и длинные ролики. Это делает их подходящими для использования в узких и компактных конструкциях, где ограничено радиальное пространство.
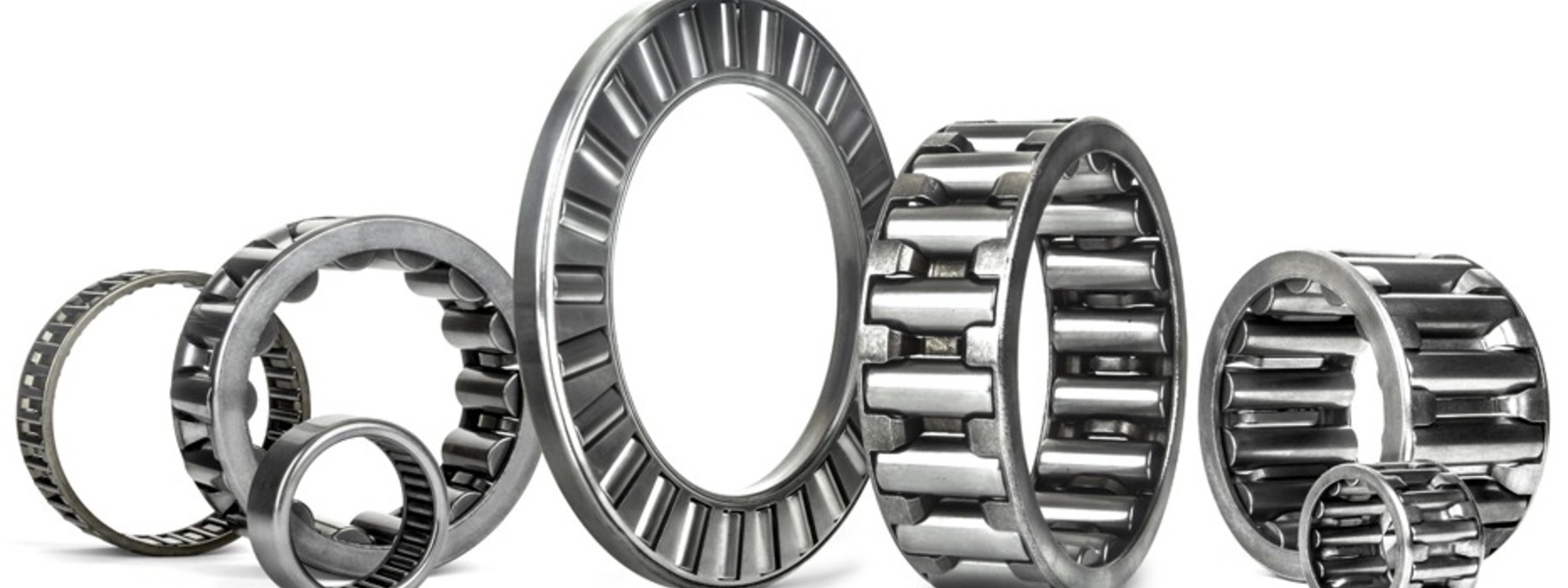
Конические роликовые подшипники
Конические роликовые способны воспринимать как радиальные, так и осевые нагрузки благодаря угловой конструкции роликов и дорожек качения.
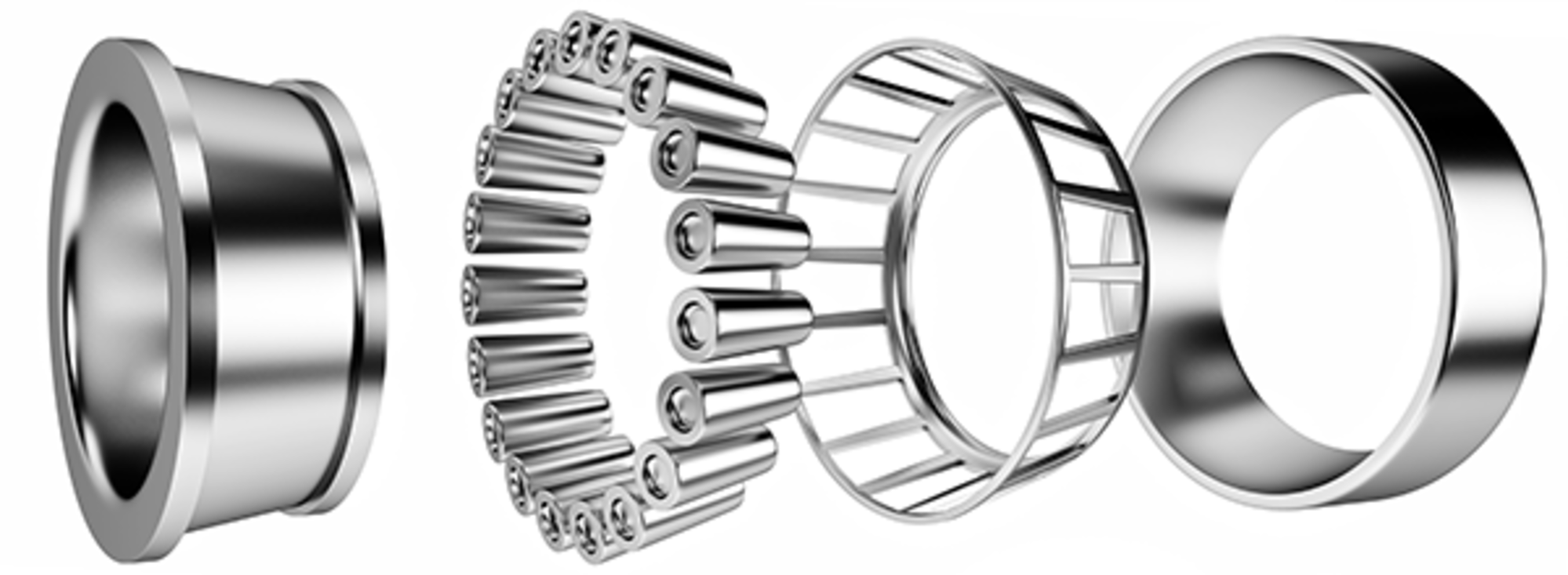
Подшипники скольжения работают на принципе скольжения одной поверхности по другой, что обеспечивает плавное движение без использования элементов качения. Они часто применяются в высоконагруженных или медленновращающихся механизмах.
Описание структуры
Ключевыми элементами любого подшипника являются вал и корпус. Вал представляет собой вращающийся элемент, на который устанавливается внутреннее кольцо подшипника. Корпус же служит стационарной опорой для внешнего кольца. Между внутренним и внешним кольцами располагаются элементы качения (шарики или ролики), которые обеспечивают низкое трение и плавность вращения вала.
Анализ внутренних и внешних элементов
Сепараторы служат для поддержания равномерного распределения элементов качения и предотвращения их контакта, что уменьшает износ и увеличивает срок службы подшипника.
Внешние элементы, включая корпус и кольца, обеспечивают механическую защиту внутренних компонентов и поддерживают их в правильном положении относительно друг друга.
Сборка и применение
Подшипники являются неотъемлемой частью практически любого механизма или устройства, где присутствует вращение или скольжение компонентов. Благодаря своим уникальным свойствам, они обеспечивают плавность хода, снижают трение и защищают механизмы от износа. Качество сборки и правильность применения напрямую влияют на долговечность и надежность работы оборудования.
Схема сборки и их конструкции
Рассмотрение схемы сборки подшипников и их конструкции представляет собой сложный процесс, который зависит от множества факторов, включая тип подшипника, его размеры, предполагаемые нагрузки и условия эксплуатации. Каждый этап сборки критичен для обеспечения высокой производительности, надежности и долговечности подшипника в условиях его работы.
Этапы сборки:
- Подготовка компонентов. Внутренние и внешние кольца, тела качения и сепараторы проходят точную механическую обработку. Точность изготовления колец может достигать от 0,001 мм до 0,005 мм, что гарантирует их идеальное соответствие и минимизирует люфт в собранном изделии.
- Установка тел качения. Количество тел качения напрямую влияет на его нагрузочные характеристики и срок службы. Например, в шарикоподшипнике с диаметром внутреннего кольца 50 мм может использоваться от 8 до 16 шариков, в зависимости от его конструкции и предназначения. Роликовые могут содержать от десятков до сотен роликов.
- Установка сепаратора. Сепараторы не только разделяют тела качения, но и способствуют их равномерному распределению и ориентации. В современных моделях сепараторы изготавливаются из металла или полимеров и могут быть спроектированы таким образом, чтобы минимизировать трение и износ.
- Смазывание. Выбор смазки и метод её нанесения критичны для долгосрочной работы подшипника. Например, для моделей, используемых в высокоскоростных приложениях, может потребоваться смазка с низким коэффициентом трения и хорошей термостабильностью. Объем смазки, который необходим подшипнику, зависит от его размера и типа; так, шариковые подшипники малого размера могут требовать всего несколько граммов смазочного материала.
- Контроль качества. После сборки каждый подшипник подвергается контролю качества, который включает проверку размеров, вращательного момента, шума и вибрации. Эти параметры могут измеряться с точностью до микрометров и микроньютон-метров, обеспечивая высокую надежность подшипника.
Применения и классификации по видам и функциональности
Подшипники классифицируются по нескольким основным критериям: типу тел качения (шариковые, роликовые, игольчатые), способности воспринимать радиальные или осевые нагрузки, а также по конструктивным особенностям (самоустанавливающиеся, упорные, радиальные). Выбор конкретного типа подшипника зависит от условий эксплуатации механизма, в котором он будет использоваться, включая скорость вращения, величину и характер нагрузок, требования к точности и долговечности.
Применение чрезвычайно широко и разнообразно. Они находят свое применение в автомобильной промышленности, авиации, сельскохозяйственной технике, железнодорожном транспорте, различных видах промышленного оборудования, а также в бытовой технике и электронике. От правильного выбора зависит эффективность, надежность и срок службы всего устройства или машины.
Практические примеры в различных механизмах
В авиации требования к подшипникам особенно высоки. Здесь используются высокоточные шариковые и роликовые подшипники, способные выдерживать экстремальные нагрузки и температуры. Например, в двигателях самолетов применяются подшипники, способные функционировать при температурах до 400°C и скоростях вращения до 25,000 об/мин. Они обеспечивают надежную работу механизмов управления и шасси, где точность и долговечность являются критически важными. В авиадвигателях могут использоваться роликовые модели диаметром от 30 мм до 400 мм, способные выдерживать осевые нагрузки до нескольких тонн.
В тяжелом машиностроении и металлургии модели скольжения находят широкое применение благодаря своей способности выдерживать высокие нагрузки и устойчивость к износу. Например, в валках горячей прокатки, где рабочие температуры могут достигать 600°C и более, используются модели скольжения с диаметрами более 1 метра и способные выдерживать радиальные нагрузки в десятки тонн. Эти подшипники часто изготавливаются из специальных бронзовых сплавов, обладающих высокой устойчивостью к тепловому расширению и коррозии.
Малогабаритные шариковые модели играют не менее важную роль в бытовой технике, обеспечивая бесшумную и плавную работу приборов. В стиральных машинах, например, используются модели диаметром от 10 до 50 мм, которые выдерживают скорости вращения барабана до 1500 об/мин и радиальные нагрузки до 2 кН. В холодильниках и кондиционерах подшипники обеспечивают бесперебойную работу компрессоров, выдерживая вибрации и температурные колебания.
Заключение
В ходе статьи были рассмотрены ключевые аспекты, касающиеся устройства, видов, конструкции и применения подшипников. Они выполняют критически важную роль в современной инженерии и технологии, обеспечивая эффективную и надежную работу машин и механизмов за счет минимизации трения между движущимися частями.
Для обеспечения надежности и долговечности ваших механизмов, рекомендуем обратиться к специалистам компании "СДМ", которые предложат нужный подшипник, а также профессиональную консультацию по выбору подходящего вида подшипников, исходя из специфики вашего оборудования и условий его эксплуатации.